1、序言
钛合金材料具有比强度高、耐蚀性和耐热性好等性能优势,被广泛应用于航空航天、武器装备等国防工业和石油化工、生物医疗等民用领域。由于钛合金具有热导率低、高温化学活性高和弹性模量小等特点,在切削加工过程中存在切削温度高、切削变形和冷硬现象严重及易粘刀等现象,导致刀具易磨损且表面加工质量差,使钛合金成为典型的难加工材料[1]。同时,钛合金构件常用的轻量化设计特点使材料去除量大,目前钛合金加工时采用的低切削用量严重制约了生产效率的提升,造成制造成本的升高。因此,实现钛合金构件的高质高效切削
加工成为制造业亟需突破的关键共性技术难题。
作为切削加工工艺研究体系中的核心要素,刀
具技术的发展可为切削加工技术带来新的变革。为
实现钛合金构件的高质高效切削加工,需要科学选用或设计开发高性能切削刀具,相关技术包括刀具材料与刀具结构设计、刀具涂层制备、刀具切削参数优选、刀具加工状态监控及切削数据库开发等,如图1所示。
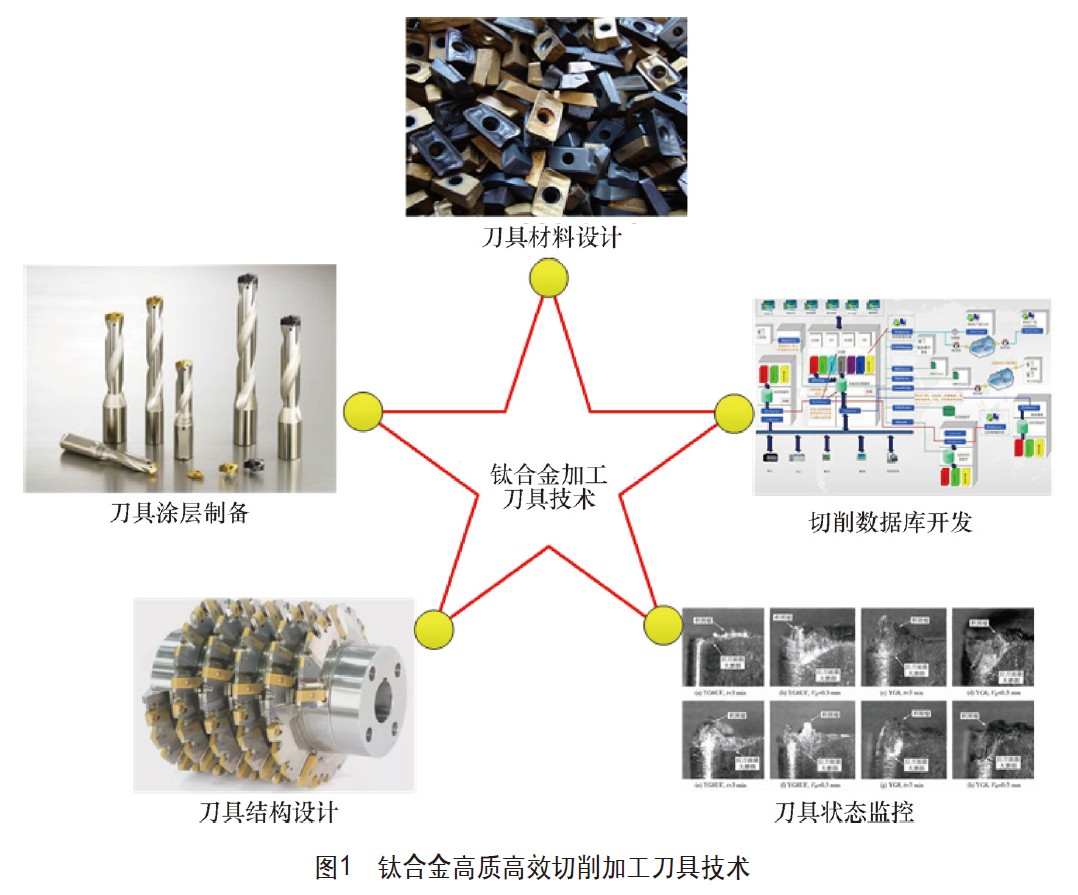
工件材料切削加工性研究是开发高性能切削刀
具的基础。基于材料切削去除机理分析,结合动态
力学性能测试、切削试验与数值仿真等手段,对钛合金切削过程热-力载荷耦合作用、材料切除变形与
失效机制、刀-屑和刀-工界面的接触与摩擦学行为
等进行理论建模及试验和仿真研究,可揭示影响钛合金切削加工性的主导因素,有助于指导钛合金高
质高效切削刀具的设计制造及选用。
在刀具材料设计方面,进行钛合金与刀具材料力学性能和理化性能的匹配性分析,建立钛合金切削加工刀具-工件作用的材料学及热力学研究体系,通过切削试验和仿真模拟探索钛合金切削过程中刀具的磨损规律并揭示刀具磨损机理,进而设计与优选适于钛合金高质高效加工的刀具材料体系。
在刀具涂层制备方面,包括新型刀具涂层材料设计选用和刀具涂层制备工艺,需针对钛合金的高化学活性特点,选用兼具减摩、耐磨与热障作用的涂层材料,并开发相应的涂层制备工艺和设备。同时,开发涂层刀具微喷砂和深冷处理等表面后处理工艺,改善刀具刃口微几何结构和涂层表层材料的微观组织,实现涂层刀具刃口和表层力学性能的协同强化。
在刀具结构设计方面,根据钛合金加工工艺特点和技术要求,开发钛合金加工特殊刃型刀具(如Wiper刀片)、整体超硬材料及密齿结构刀具等,可以实现其高效率切除与高表面质量加工。在刀具切削参数优选方面,可根据钛合金表面加工质量、加工效率与加工成本等经济技术指标,优化切削参数,实现钛合金高质高效加工。同时,开发刀具加工状态监控技术并建立切削加工数据库,实现加工过程状态监控和工艺参数的智能推送等功能,助推智能制造的发展和工程化应用。
2、钛合金切削刀具材料
在切削加工过程的高温影响下,钛元素具有高的化学活性,如何避免钛合金与刀具材料元素之间的剧烈粘结扩散,是选择钛合金加工刀具以及刀具材料设计时需考虑的首要因素。
钨钻类硬质合金(YG类,即ISO标准的K类,由WC和Co构成)是加工钛合金常用的刀具材料。
研究对比YG、YT、YW三种硬质合金刀具加工钛合金时的刀具磨损机理[2],发现低速切削时三类刀具均以粘结磨损为主,高速切削时YG类刀具仍以粘结磨损为主,但YT类刀具在粘结磨损的同时伴随产生一定的氧化磨损和扩散磨损,YW类刀具则是三种磨损机理占据同等地位,因此在低速切削钛合金时可优先选用YG类硬质合金刀具,高速切削时可选用YW类或YG类硬质合金刀具。除了与刀具中的Co含量有关外,影响钛合金切削刀具性能的另一主要因素是晶粒度,细化且均匀分散的WC硬质相和Co粘
结相可增大两相粘结面积,不仅有助于提高硬质合金的抗弯强度和冲击韧性,同时还可保证硬质合金的高硬度和良好的耐磨性。当WC晶粒的平均尺寸在0.8~1.4μm时,钨钴类硬质合金刀具表现出较好的抗磨损性能[3]。
采用普通晶粒尺寸的硬质合金刀具加工钛合金时刀具寿命通常较短,导致切削速度只能在低于50m/min范围选取,加工效率较低。肯纳刀具推出的由细晶粒碳化钨(含钴6%)组成的K313材质基体,兼具高的热硬度和良好的抗塑性变形能力,有效保证了刀具韧性和均匀的后刀面磨损,在精加工阶段切削速度在100m/min左右时刀具仍具有正常的加工寿命。山特维克可乐满H13A(HW)和伊斯卡IC20非涂层硬质合金刀具材料具有良好的抗粘结磨损性和高韧性,适用于航空工业钛合金零部件加工。
超硬刀具材料如聚晶立方氮化硼(PCBN)和聚晶金刚石(PCD)可以实现钛合金材料的高速、高精度和高稳定性加工。对比分析不同刀具材料在高速车削钛合金时的磨损差异,包括未涂层硬质合金、TiAlN PVD涂层硬质合金以及PCBN等,发现PCBN刀具材料在高切削速度、低进给量、低背吃刀量下切削钛合金时可以获得较平稳的切削力和较低的加工表面粗糙度值[4];PCD刀具在切削速度为200m/min以上加工钛合金时,仍然可以保持较好的刀具使用寿命和加工表面质量。因此,PCBN和PCD等超硬刀具材料适用于钛合金的精加工和高速加工。
3、刀具涂层工艺
开发适于钛合金加工的涂层刀具有助于提升加工效率和延长刀具寿命。刀具涂层材料具有硬度高、耐磨性好、化学性能稳定、耐热耐氧化和热导率低等特性,相比未涂层刀具可以提高刀具寿命3~5倍以上,提高切削速度20%~100%,提高加工精度0.5~l级,并可大幅降低刀具成本[5]。
通过对比物理气相沉积P V D 涂层(TiN+TiAlN)硬质合金刀具和化学气相沉积CVD涂层(TiN+Al2O3+TiCN)硬质合金刀具的钛合金高速铣削性能,发现PVD涂层刀具的使用寿命大于CVD涂层刀具,表现出更优异的切削性能[6]。森拉天时的CTC5240刀片通过结合高粘结性细晶WC基体与超薄PVD涂层,在钛合金高效加工中表现出良好的耐磨性和使用寿命。对于新型单涂层材质,硬质薄膜材料CrN涂层和Al2O3涂层具有优异的耐磨损性能和抗氧化附着能力,可适用于钛合金等难加工材料切削。瓦尔特刀具利用PVD涂层方法在刀具基体上沉积Al2O3硬质镀层,该涂层制备工艺热载荷小,可在提高刀片韧性的同时保持Al2O3镀层的高硬度、良好耐热性和耐磨损等性能,减少了出现积屑瘤的倾向,适合钛合金高速加工。此外,AlCrN、CrSiN和AlCrSiN等涂层亦适用于钛合金加工,研究表明高速干切削钛合金时,AlCrSiN涂层刀具的
切削寿命超过无涂层刀具,切削力、切削温度和加工表面粗糙度指标均优于无涂层刀具[7]。近年来,MoS2和WS2等软涂层刀具也为钛合金加工提供了新的选择。
刀具涂层后处理技术可以进一步提升刀具的切削性能。以PVD TiAlN涂层刀具为例,通过对TiAlN涂层进行干式微喷砂强化后处理,并基于断裂力学理论分析喷砂时间和喷砂压强对刀具涂层表面粗糙度和表层硬化深度的影响,证明微喷砂后处理工艺可以显著改善TiAlN涂层的表面完整性,使涂层显微硬度较微喷砂处理前提高15%以上,从而提高涂层刀具的耐磨损性能并延长使用寿命[8]。利用湿式微喷砂对CVD TiN/A12O3涂层刀具进行后处理,发现喷砂时间、磨料类型和磨粒直径等微喷砂工艺参数对涂层刀具几何形貌、力学性能及使用寿命具有重要影响,经过微喷砂后处理可有效去除涂层表面的大颗粒缺陷,降低刀具涂层表面粗糙度值,使刀具平均寿命提高27.5%[9]。
深冷处理可以通过改变刀具材料的微观组织而改善其力学性能,近年来被逐渐尝试应用于刀具后处理强化。通过研究深冷处理对TiAlN涂层刀具微观组织及力学性能的影响,发现深冷处理后硬质合金基体中η相碳化物的含量显著增加,有利于提升涂层与基体的结合强度以及基体材料硬度,且深冷处理温度降低时涂层与基体的结合强度提高;进一步对比深冷处理前后的TiAlN涂层刀具的车削寿命,表明-190℃深冷处理24h后的刀具寿命相比未深冷处理刀具提高了34.8%[10]。同样,深冷处理PVDTiAlN/NbN等其他类型涂层的硬质合金铣削刀具,可提高其在钛合金加工时的刀具耐磨性能。
4、刀具结构设计
采用新刀具结构设计实现难加工材料的高质高效加工是现代企业提高经济效益的重要途径。刀具材料改进是刀具技术发展的主线,而在现有刀具材料基础上,通过刀具几何结构设计改善切削性能也是提高切削效率和加工质量的有效途径。国际生产工程科学院CIRP指出,“由于刀具材料的改进,刀具许用切削速度每隔10年提高1倍,而由于刀具几何结构的改进,刀具寿命每隔10年则提高近2倍”。
相比切削刃数、刀具角度等宏观结构,刀具切削刃的微几何特征是影响其切削性能的更直接因素。山特维克可乐满的CoroMill® Plura整体式立铣刀利用多刃型结构设计可实现高进给、小径向切削深度和高切削速度的钛合金加工,大幅度减少切削热量的产生,提供了在航空航天钛合金整体叶盘加工中的刀具解决方案。瓦尔特的高进给铣刀M4002刀片的后刀面波浪设计,提高了钛合金的切削加工质量,并使刀具寿命提高1倍。德国来宝精工设计的全刃口新型切削刃采用三角斜度槽型设计,可实现钛合金抗振动高进给加工,效率提高3倍,寿命延长50%。
Wiper刃型有助于实现钛合金材料高速度、大进给、大切削深度的高效切削。其中,瓦尔特Xtratec®可转位钻头B4213通过使用Wiper修光刃有效改善了表面加工质量。通过对比Wiper刀片与普通刀片铣削钛合金Ti-6Al-4V的加工性能[11],发现在获得相同表面质量时,Wiper刀片可以采用大进给量切削,相比普通刀片切削效率提高1倍。利用形状因子法对刀具刃口几何进行参数化表征,可定量化揭示刃口微结构对加工表面残余应力等完整性指标的影响规律,为刀具的刃口结构设计与制备提供指导[12]。
钛合金切削加工过程中容易在切削区域积聚大量的切削热,严重损害加工工件的尺寸精度与服役性能。为解决切削过程中切削热量高且难以耗散的问题,山特维克可乐满、肯纳和瓦尔特等刀具厂商提出了高压内冷却加工技术和相应结构的刀具。通过对比干切削、浇注式冷却以及高压冷却三种加工环境下的钛合金车削试验,分析切削介质与出液孔位置对切削力与切削温度的影响规律,发现刀具冷却结构会影响钛合金的加工表面形貌、微观组织和力学性能,利用高压内冷却刀具可以有效解决钛合金切削过程中的热量累积和散热问题,且前、后刀面双出液孔刀具结构对加工表面完整性的改善尤为显著[13]。
5、刀具加工状态监控及切削数据库
刀具切削过程的智能监控是实现智能制造的关键技术。随着人力成本的不断提高和对自动化生产的迫切需求,无人化车间与黑灯工厂将越来越普遍。刀具切削过程智能监控技术可以实时感知刀具的工作状态,在掌握刀具是否存在异常的同时能够自动调整工艺参数;当发现刀具工作状态出现故障时及时做出预警及决策,从而提高生产效率并保障加工质量。因此,无人干预条件下的刀具状态监控,是实现切削加工自适应调整的基础,也是机床设备安全工作的保障。
刀具在切削过程中的磨损、破损行为和刀具振动是影响加工表面质量的重要因素。刀具磨损是切削过程中刀具的正常损耗形式,刀具磨损量增加易导致表面加工质量变差、加工精度下降等,从而造成废品率上升;刀具破损是刀具的非正常损坏,破损严重时将急剧恶化加工表面质量甚至损坏加工设备[14]。因此,需要对刀具的磨损、破损状态进行有效实时监控,并根据刀具工作状态给出换刀、停车等指令或优化后续工艺参数。刀具振动是切削刀具与工件之间相互作用的结果,不稳定的刀具振动将影响切削系统的加工稳定性,振动严重时(如颤振)可能损坏工件加工表面并产生刀具崩刃。刀具振动问题影响因素众多、时变性强且建模过程复杂,一般难以完全避免。
开发有效的刀具加工状态监测技术对于实现切削过程的自动化运行、保证零件加工质量、保护机床设备安全以及提高生产车间的智能化水平具有重要意义。现有智能刀具主要通过安装某一种或几种传感器实现刀具状态监测功能,例如采用压电陶瓷薄膜或声表面波传感器可以实时监测刀具磨损,利用集成热电偶可以测试切削温度等。随着智能制造技术的发展,更便捷且高效地在切削刀具或加工系统中集成不同功能传感器,并基于多传感器融合技术和人工智能算法对复杂切削状态进行监测,实现刀具状态监控与数控加工系统的多维交互,从而主动调整加工参数并充分发挥刀具与机床的工作效能,将是未来智能刀具和智能制造的发展趋势[15]。
切削数据库是利用计算机技术存储刀具和加工工艺数据,按照生产需求迅速获取特定加工场景下所需刀具信息和切削参数的数据化管理工具。利用切削数据库技术可以根据生产约束条件优化切削工艺,实现高效高质切削加工。数据库技术将先进的计算机技术与传统制造业相融合,实现制造资源信息的数据化和结构化管理,符合制造业数字化的发展趋势。基于实验室试验数据、车间生产经验数据以及文献手册数据等,可开发出涵盖车、铣、钻和镗等系列化加工工艺的刀具数据库系统,为用户提供优化的钛合金等难加工材料的切削刀具、切削用量等加工信息,从而有效提高生产效率。基于加工特征分类建立不同类型零件的加工数据库系统,同时结合实例推理技术,将已有切削加工积累的切削数据和经验模型存储在数据库中,可为新加工案例提供数据基础和参考解决方案[16]。进一步将切削数据库系统与CAM软件集成,可以为数控编程快速准确地提供切削数据,有利于缩短生产制造周期,提高产品的市场竞争力。
6、结束语
随着切削刀具技术的发展,钛合金高质高效切削加工技术正在逐渐成熟,在钛合金加工刀具材料与刀具结构设计、刀具涂层制备、刀具加工状态监控和数据库开发等方面均取得了一定进展。
在制造业快速发展的背景下,航空航天、汽车及能源等行业不断涌现的新材料对切削加工技术提出了更高的要求,推动刀具材料和刀具结构的持续创新。高质高效刀具的开发成为革新加工工艺、提高加工效率和加工质量、降低加工成本的重要源动力。随着五轴工具磨床加工精度的提高以及超快激光等高能束加工技术的发展,复杂结构刀具的精密制造逐步成为现实,从而为改变刀具结构设计提供了技术基础,将使刀具切削性能得以持续提升。
同时,在智能制造技术的推动下,“智能刀具”和“智能加工”逐步得到重视并成为国际研究的热点和前沿问题,先进微电子和传感技术在切削刀具中的进一步应用将有助于加强刀具加工过程的实时监测以及智能控制。
因此,在制造业发展的需求牵引和机械、材料以及信息技术等交叉学科的协同驱动下,开发具有更优切削性能且兼具智能化功能的高性能切削刀具,将成为未来发展的重要方向。
参考文献:
[1] WANG B, LIU Z, CAI Y, et al. Advancements inmaterial removal mechanism and surface integrity ofhigh speed metal cutting: A review[J]. International
Journal of Machine Tools and Manufacture, 2021(166):103744.
[2] 姜增辉,王琳琳,石莉,等. 硬质合金刀具切削Ti6A l4V的磨损机理及特征[J]. 机械工程学报,2014,50(1):179-184.
[3] LIANG X, LIU Z, WANG B. Physic-chemical analysisfor high-temperature tribology of WC-6Co againstTi-6Al-4V by pin-on-disc method[J]. Tribology
International, 2020(146):106242.
[4] LINDVALL R, LENRICK F, PERSSON H, et al.Bushlya. Performance and wear mechanisms of PCDand pcBN cutting tools during machining titanium
alloy Ti6Al4V[J]. Wear, 2020(454):203329.
[5] ZHAO J, LIU Z, WANG B, et al. Tool coatingeffects on cutting temperature during metal cuttingprocesses: Comprehensive review and future research
directions[J]. Mechanical Systems and SignalProcessing, 2021(150):107302.
[6] 徐锦泱,郑小虎,安庆龙,等. 高速铣削TC6钛合金的刀具磨损机理[J]. 上海交通大学学报,2012,46(7):1037-1042.
[7] ZHANG Q, XU Y, ZHANG T, et al. Tribologicalproperties, oxidation resistance and turningperformance of AlTiN/AlCrSiN multilayer coatings by
arc ion plating[J]. Surface and Coatings Technology,2018(356):1-10.
[8] 徐培利,刘战强. 微喷砂后处理工艺对涂层刀具性能的影响规律[J]. 现代制造工程,2015(7):85-92.
[9] LIU C, LIU Z, WANG B. Modification of surfacemorphology to enhance tribological properties for CVD coated cutting tools through wet micro-blasting
post-process[J]. Ceramics International, 2018, 44 (3):3430-3439.
[10] 冷可,刘战强,王兵. 深冷处理对TiAlN涂层刀具微观组织及力学性能的影响[J]. 工具技术,2020,54(12):10-14.
[11] EHSAN S, KHAN S A, REHMAN M. Defect-freehigh-feed milling of Ti-6Al-4V alloy via a combinationof cutting and wiper inserts[J]. International Journalof Advanced Manufacturing Technology, 2021, 114(1): 641-653.
[12] DENKENA B, LUCAS A, BASSETT E. Effects ofthe cutting edge microgeometry on tool wear and itsthermo-mechanical load[J]. CIRP Annals, 2011, 60
(1):73-76.
[13] LIU W, LIU Z. High-pressure coolant effect on thesurface integrity of machining titanium alloy Ti-6Al-4V: a review[J]. Materials Research Express, 2018, 5(3):032001.
[14] WANG B, LIU Z. Influences of tool structure, toolmaterial and tool wear on machined surface integrityduring turning and milling of titanium and nickelalloys: a review[J]. International Journal of AdvancedManufacturing Technology, 2018, 98(5):1925-1975.
[15] BAROROH D K, CHU C H, WANG L. Systematicliterature review on augmented reality in smartmanufacturing: Collaboration between humanand computational intelligence[J]. Journal ofManufacturing Systems, 2021(61): 696-711.
[16] 李晓君,刘战强,沈琦,等. 基于加工特征的整体叶盘数控编程与加工参数优化[J]. 组合机床与自动化加工技术,2019(3):153-156.
相关链接